基于K型熱電偶的輸送帶接頭硫化感應加熱系統(tǒng)的
發(fā)布時間:2021-02-24
瀏覽次數(shù):
摘要:傳統(tǒng)的輸送帶接頭硫化加熱方式存在加熱不均勻、時間長、效率低等問題,為此提出了一種.基于電磁感應的輸送帶接頭硫化加熱系統(tǒng)。搭建了接頭硫化感應加熱系統(tǒng)的整體框架,然后通過COMSOL軟件仿真得出通電線圈作用下的加熱板溫度分布云圖,結合仿真結果,在鋼板.上的不同位置布置
K型熱電偶,通過
多路溫度記錄儀將測得的溫度數(shù)據(jù)記錄下來。結果表明:所設計的感應加熱系統(tǒng)能夠使硫化加熱板均勻發(fā)熱,且由K型熱電偶與多路溫度記錄儀構成的溫度監(jiān)測系統(tǒng)能夠對數(shù)據(jù)進行可靠的采集與處理。
0引言
輸送帶接頭硫化機將接頭兩端無連接的鋼絲繩在高溫高壓下用橡膠連接起來,形成一條完整的輸送帶甲。接頭的強度主要取決于硫化階段對膠料與鋼絲繩物理成形的加熱控制,而作為硫化機主要部件的加熱板的表面溫度均勻性會影響到接頭的質量,對于輸送帶接頭的硫化加熱,目前存在多種方式:電加熱、蒸汽加熱.導熱油加熱等2.
蒸汽加熱的缺點是在加熱過程中,升溫歷程存在滯后性,可控性較差;電加熱容易造成電能的浪費且升溫較慢;導熱油加熱的缺陷在于整體結構設計較復雜。對于橡膠的硫化,有學者通過調整電磁的熱參數(shù)解決了輪胎硫化的不均勻問題,但是對于電磁感應加熱方式應用于輸送帶接頭硫化的研究較少。
本文搭建了以電磁加熱控制器調節(jié)線圈和電磁參數(shù)為基礎的輸送帶接頭硫化感應加熱系統(tǒng),通過COMS0L仿真得出感應加熱下的熱板溫度分布規(guī)律,研究加熱板發(fā)熱的均勻性,并在實驗平臺中的加熱板不同位置布置K型熱電偶,以多路溫度記錄儀實時監(jiān)測溫度數(shù)據(jù)并顯示出來,用以驗證仿真結果的準確性。溫度監(jiān)測的結果表明電磁感應加熱方式能夠有效解決硫化加熱不均勻的問題。
1輸送帶接頭硫化感應加熱系統(tǒng)的組成
電磁感應加熱系統(tǒng)主要由線圈、加熱鋼板、電磁加熱控制器以及溫控儀組成,電磁加熱控制器與溫控.儀相連,溫控儀的設定溫度為150℃,此為硫化溫度,其作用是使電磁加熱控制器加熱的溫度穩(wěn)定在±3℃范圍內(nèi)波動,使加熱控制器以脈沖形式對鋼板加熱,達到均勻硫化的效果。
1.1電磁加熱控制器
如圖1所示,采用半橋單管5-8kW功率的電磁加熱控制器,它可以將低頻三相交流電以高頻形式輸出,具有IGBT過流保護功能D,同時有輸出過流保護自動調節(jié)負反饋的功能(其中5kW功率下的電流保護點為22A,8kW功率下的電流保護點為30A),其內(nèi)部采用高速輸出電流霍爾傳感器,能更精確地檢測相位和電流大小4。采用高性能IGBT驅動芯片驅動,可以自動識別負載及鎖相功能,以使負載端得到最高功率因數(shù),也使電路精確控制在弱感區(qū)保持高效率工作。控制面板上有功能鍵,能夠顯示諧振狀態(tài)、頻率、電流、ICBT溫度等。
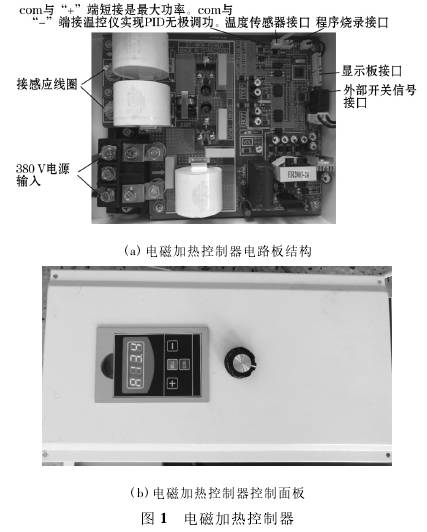
1.2線圈和加熱鋼板
電磁加熱控制器可以通過控制流過線圈電流的大小和頻率來控制加熱鋼板的升溫速率,線圈通電后,由于交流電的影響,在其內(nèi)外會產(chǎn)生與電流變化.相同的交變磁場,鋼板置于這一范圍內(nèi),鋼板上就會產(chǎn)生與線圈相反的感應電流,感應電流在鋼板上會形成封閉的回路,一-般被稱為渦流,渦流的作用是使電能轉換為熱能,鋼板才會發(fā)熱國。接頭硫化感應加熱系統(tǒng)工作流程圖如圖2所示。
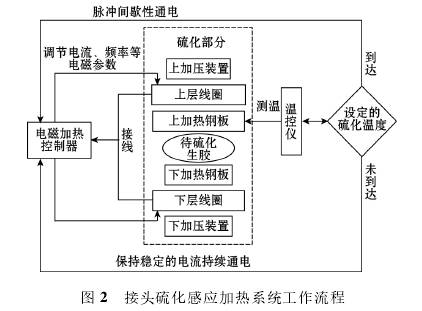
按照電磁加熱控制器上的電路板的接線方式,依次將電磁加熱控制器與電源線、溫控儀和線圈相連,將溫控儀調節(jié)到硫化所需的溫度,接通總電源后調節(jié)電磁參數(shù)即可讓系統(tǒng)正常工作,溫控儀上設有傳感器,將該傳感器置于鋼板上,用于探測鋼板的溫度是否達到所需的硫化溫度,若未達到硫化溫度,會控制加熱器為線圈繼續(xù)供電,直至測得鋼板溫度達到硫化溫度,若已升溫至目標值,溫控儀將會使電磁加熱控制器間斷性地提供電流,以脈沖的形式進行加熱,使溫度保持在一穩(wěn)定值。所設計的加熱系統(tǒng)整體結構如圖3所示。
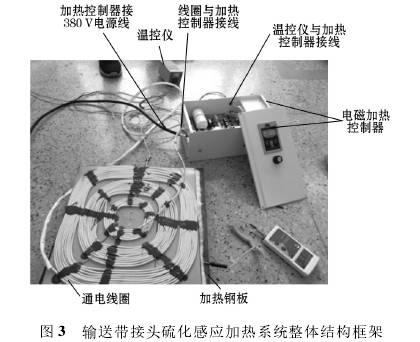
2加熱仿真模型的建立與分析
電磁感應加熱仿真模型主要簡化為線圈和加熱鋼板,由電磁加熱控制器的參數(shù)設定線圈的電感量,布置好線圈的排布方式,調節(jié)線圈與加熱鋼板之間的距離,建立線圈和鋼板的三維模型(圖4),表1為鋼板的物理性能參數(shù)。

在COMSOL軟件中研究線圈通電狀態(tài)下熱板的升溫規(guī)律。鋼板的尺寸設定為400mmx400mmX10mm。仿真的求解域是電磁場和溫度場的耦合場,在軟件中設置電磁參數(shù),包括電流大小、頻率、線圈匝數(shù),在頻域-瞬態(tài)的研究中將電磁損耗作為溫度場求解的初始條件,最終可以得到感應電流的分布情況以及溫度隨時間的變化過程。仿真選取多種參數(shù)下的組合,設定線圈匝數(shù)為固定值,將電流大小和工作頻率進行組合,設置的參數(shù)組合如表2所示。
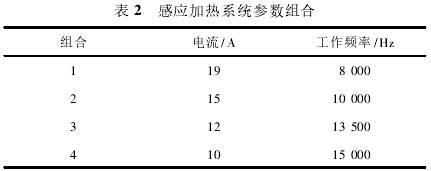
對表2不同組合下的線圈工作參數(shù)進行設置,可以得出4種條件下鋼板的升溫規(guī)律和溫度分布云圖,如圖5所示。
可以看出,由于感應電流的作用,鋼板表面的溫度會逐漸升高,由于線圈中部位置的磁場強度近似為邊緣端部的2倍,所以鋼板4個邊角處的穩(wěn)定溫度是最低的,由于渦流分布是由中心向邊緣逐漸擴大,從而鋼板中心位置處會出現(xiàn)加熱死區(qū),即中間部分某—區(qū)域的溫度低于其周圍溫度。圖5中4種工況下的溫度分布趨勢基本--致,電流越小,中間加熱死區(qū)的面積也逐漸減小,與周圍區(qū)域的溫差也逐漸縮小。圖中沿加熱死區(qū)向鋼板邊緣端部過渡,會出現(xiàn)溫度的極大值,原因是由于此處磁通密度較大,所產(chǎn)生的感應電流在此處匯聚密集,導致溫度升高較快。由邊角向中.心區(qū)域分析,溫度是逐漸升高的,由仿真看出,隨著電流的減小和頻率的增大,鋼板表面的整體溫差是逐漸.縮小的。
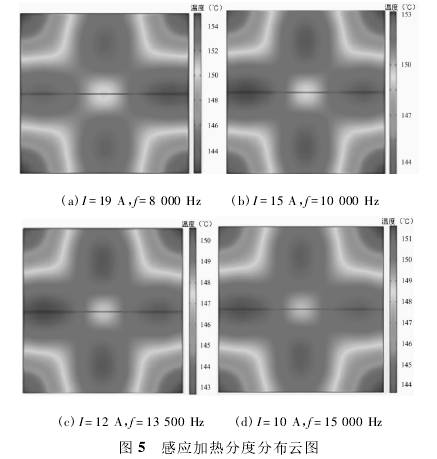
3輸送帶接頭硫化加熱系統(tǒng)的溫度監(jiān)測
3.1K型熱電偶與多路溫度記錄儀
如圖6所示,多路溫度記錄儀主要由觸控液晶屏、按鍵、ARM微處理器為核心的主板、主電源、智能通道板、大容量FLASH等構成。記錄儀的采樣周期為1s,能實時顯示數(shù)據(jù)圖、柱狀圖、曲線圖等。可以根據(jù)所布置的K型熱電偶的數(shù)量,設置通道數(shù)目,對于每--路的溫度補償,支持補償信號的輸入,能夠提供多種補償模式”。含有與上位計算機通訊的標準.接口,將數(shù)據(jù)傳輸至計算機中,便于對后期數(shù)據(jù)的收集與整理。
K型熱電偶主要包括感溫元件、接線盒與保護套管等,將其與多路溫度記錄儀配套使用甲,可以保證溫度數(shù)據(jù)采集的準確性,主要用于監(jiān)測電磁感應加熱方式下加熱鋼板的溫度變化情況。
針對不同位置處的溫度變化,結合仿真的4種電流下的溫度分布云圖,對多個K型熱電偶進行排布,將其置于加熱板的下表面,測溫點的布置如圖7所示。
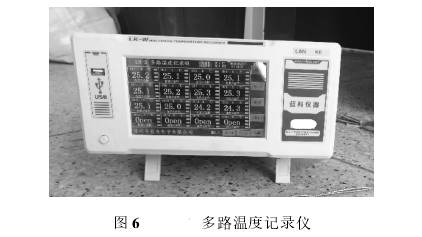
選取了12個測溫點,分別對應溫度監(jiān)測系統(tǒng)的12個通道。研究沿鋼板中心線方向(測溫點1、2、3)、對角線方向(測溫點4.5、7)、中心區(qū)域(測溫點6、7、8、9)以及鋼板下半部分(測溫點9.10、11、12)的溫度變化趨勢,可以得到不同電流數(shù)值的工作狀態(tài)下的溫升曲線。

3.2溫度數(shù)據(jù)的監(jiān)測及分析
將傳感器排布到鋼板上,從平板硫化機的下加壓板向上,依次布置下加熱鋼板、待硫化生膠、上加熱鋼板、上加壓板,并按順序對所需儀器進行接線,搭建好實驗平臺,輸送帶接頭硫化感應加熱的溫度監(jiān)測系統(tǒng)如圖8所示。
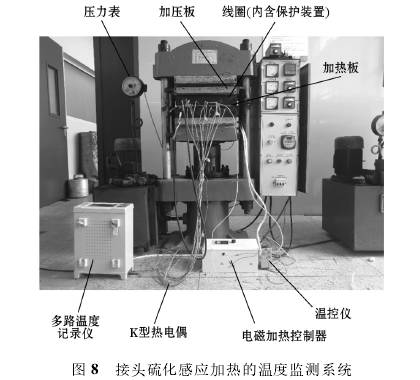
實驗平臺搭建完成后,扳動電源開關,電磁加熱控制器開始工作。調節(jié)其控制面板.上的螺旋變位旋.鈕,可以對電流、頻率、電壓等參數(shù)值進行設定。調整不同的電流(10、12.15、19A)后,多路溫度記錄儀會記錄溫度數(shù)據(jù)的變化(圖9),得到沿中心線方向在不.同電流下的溫度變化。

分析沿中心線位置的溫度變化,電流為10A和12A時,1點位置溫度最高,觀察圖5的仿真結果,1點處于整塊鋼板溫度最高區(qū)域的核心部位,2點位于高溫區(qū)域的邊緣,3點處于加熱死區(qū)的邊緣,所以3點溫度最低,隨著電流的增大,電流由12A增大至15A,高溫區(qū)域的熱量分布會向鋼板邊角擴散,導致測溫點1處的溫度低于2處的溫度,與加熱死區(qū)接觸部分的熱量逐漸向外圍擴散,導致測溫點3處的溫度較高,隨著時間的推移最終高于2處的溫度,由圖9(d)看出,當電流為19A時,3個測溫點在升溫過程中的溫差較大,強電流不易于保證升溫的均衡性。
然后分析沿對角線方向(4、5、7點)在不同電流下的溫度變化,得到如圖10所示的曲線圖。
由圖10分析可知,當電流由10A向19A變化時,4點溫度是最低的,原因是該點在鋼板的邊緣位置,受電磁感應影響較小,測溫點7表示的是鋼板的最中心位置,10A電流條件下,當熱板溫度穩(wěn)定后,測溫點5的溫度高于7點,說明此時加熱死區(qū)的面積較小,弱電流會使中心加熱死區(qū)面積縮小,隨著電流由12A向15A增大,中心加熱死區(qū)的面積逐漸擴大,測溫點5逐漸成為了加熱死區(qū)的邊緣部位,邊緣部位熱交換頻繁,故此時其溫度低于測溫點7,當電流為19A時,如圖10(d)所示,在強電流的作用下,由于加熱死區(qū)外圍溫度升溫較快,5點受其他區(qū)域熱傳導的影響,溫度逐漸高于7點。
分析沿對角線區(qū)域的溫度變化,隨著電流的增大,在鋼板加熱過程中,不同點升溫的快慢也不一--致,4點溫升波動幅度較大,因為4點處于鋼板邊角部位,受感應電流影響較小,且與其他區(qū)域進行熱交換不明顯。電流增大的過程中鋼板的升溫時間逐漸縮短,且溫度不均勻性也越明顯。4種電流下(10、12、15、19A)下鋼板升溫至硫化溫度所需的時間分別是29、25、.18、12min。
分析中心區(qū)域處(6.7.8.9點)在不同電流下的溫度變化,得到如圖11所示的曲線圖。分析在熱板中心區(qū)域,也就是加熱死區(qū)部位的溫度,以測溫點6、7、8、9的溫度變化來反映。由圖11中可以得出,6、8 點位于加熱死區(qū)邊緣,隨著電流的變化,加熱死區(qū)面積也在改變,所以與周圍區(qū)域進行的熱交換較頻繁,6點和8點能夠較快速地吸收高溫區(qū)域的溫度,所以兩者溫度變化很頻繁。
最后分析鋼板下半部分(9、10、11、12點)在不同電流下的溫度變化,得到如圖12所示的曲線圖。
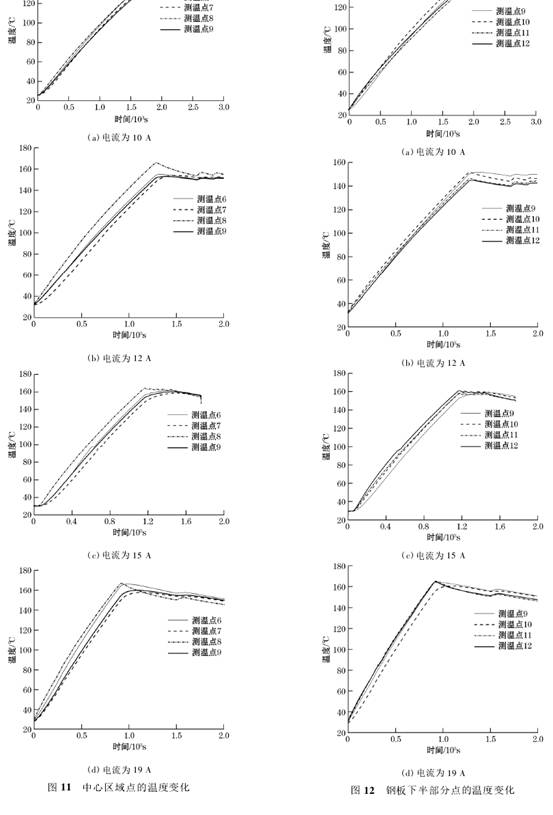
分析在熱板下部分中間區(qū)域,以測溫點9、10、11、12的溫度變化來反映。由圖12中可以看出,最終溫度穩(wěn)定后,測溫點9、10的溫度高于測溫點11、12的溫度。這是由于點11位于鋼板下部邊角與高溫區(qū)域的接觸處,此處是整塊鋼板溫差最大處,測溫點12位于接近鋼板邊緣處,此位置與空氣之間會產(chǎn)生部分熱交換,故此處溫度偏低。而測溫點9接近鋼板中心,且其.周邊溫度熱量較均衡,熱損失較少,測溫點10是鋼板.熱量最大處向周邊蔓延的過渡點,所以兩者溫度較測溫點11和12高。
結合圖9~圖12的數(shù)據(jù),最終溫度穩(wěn)定后均能保持較小的溫差,體現(xiàn)了加熱效果的均勻性。
4結束語
針對現(xiàn)有輸送帶接頭硫化加熱方式存在的加熱不均勻、接頭質量差、加熱時間長等問題,本文以電磁.加熱控制器為基礎,設計出了一種基于電磁感應的加.熱系統(tǒng),并通過仿真分析,建立了基于K型熱電偶和多路溫度記錄儀的12通道監(jiān)測系統(tǒng),得到了鋼板不同位置的溫度變化規(guī)律和溫升曲線,證明了此種加熱方式能夠使鋼板快速達到硫化溫度,且能使溫度均衡分布,調節(jié)相應電磁參數(shù)可以最大限度降低溫差,所設計的溫度監(jiān)測系統(tǒng)能準確地采集處理溫度數(shù)據(jù),這可以為后期構建高可靠性硫化系統(tǒng)的全息表達方式、形.成硫化系統(tǒng)智能監(jiān)測平臺提供了參考。